- Home
- Products
- Car Radiator Making Machine
- Aluminum Radiator Tube Mill (High Frequency)<)
Aluminum Radiator Tube Mill (High Frequency)<)
Description of High Frequency Aluminum Radiator Tube MillThis series of high frequency aluminum radiator tube mills is capable of producing aluminum radiator flat tubes, condenser/evaporator header pipes, intercooler flat tubes, etc.
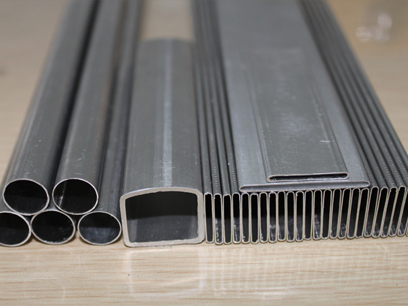
Our tube mills can 100% replace those aluminum pipe mills from Schoeler Germany, Millmaster USA, or Japan.
Production Flow of High Frequency Aluminum Radiator Tube Mill- Aluminum strip reel loading by vacuum absorber loading device (optional)
- Aluminum strip decoiling by active decoiler
- Aluminum strip feeding by synchronization feeder with buffer
- Pre-forming by pre-forming mould section
- Welding by solid-state high-frequency welder
- Squeezing by ceramic rollers
- Burr removing
- Size fixing by size-fixing mould section
- Cutting to length by non-stop flying saw cutter
- Special roller designing and adjusting technology for various aluminum tube forming.
- Max. production speed 150m/min
- High quality solid state high-frequency welder, less electric consumption, smaller internal burr
- Online cut-to-length, no need secondary processing
- Special cutting device, supper high speed cutting catching the whole line speed
- 300~375 cuts/min @400mm length
- 160~200 cuts/min @750mm length
- 120~150 cuts/min @1000mm length
- 40~50 cuts/min @3000mm length
- 20~25 cuts/min @6000mm length
Item | Data |
Suitable material | Pure aluminum or aluminum alloy 4343/3003/7072 or 4343/3005/7072, with/without cladding |
Applicable flat aluminum tube size | Width: 16~32mm Thickness: 1.8~2.2mm Wall thickness: 0.26~0.30mm |
Suitable aluminum pipe length | 300~6000mm |
Applicable aluminum strip coil size | Max. OD: 1900mm ID: 290~310mm Max. Weight: 900kg |
Production speed | Max. 150m/min |
Cutting speed | Max. 400 cuts per minute |
Cooling method for welder | Air cooler + water chiller |
Cooling method for rollers | Recycling liquid type coolant |
Transmitting method | Coupling + reducer distributors |
Tube bow | ≤0.5mm @500mm length |
Tube twist | ≤0.3mm @300mm length |
Cutting end inclination | ≤0.3mm |
Cutting burr height | ≤0.08mm |
Cut-to-length precision | ≤ ±0.3mm |
Life of cutting blades | More than 0.2 billion cuts |
Duration for changing rollers | One hour by 4 workers @ cassette changing method |
Duration for changing tube width | ≤ 15min |
High-frequency power | 400kHz, 100kVA |
Total electric power | About 160kVA |
Total electric consumption | About 80 kW·h |
Air source | 0.5-0.7MPa, 0.8m3/min |
Noise level | ≤78dB (@2m away) |
Pollution | Welding smoke & dust collecting, no liquid pollution discharged |
Total weight | About 16 Tons |
Whole line dimension | About 30m x 5m x 3.5m (including run-out rack) |
Inquiry Form